A German wood-based insulation product has entered the US market and found its way into new superinsulated homes. Agepan THD (AH-ga-pahn) doesn’t look at all revolutionary or high-tech, but it hits a sweet spot that makes it very useful.
It’s basically a two-inch-thick wallboard with tongue-and-groove edges, made of fine wood fibers lightly compressed and impregnated with just enough wax to make it highly water-resistant while leaving it vapor-permeable. It’s much less dense than what you think of as wallboard, though, with that added “fluff” factor giving it insulation value. It has a polyurethane binder holding it together, but is formaldehyde-free. It’s a more “natural” alternative to rigid foam sheathing.
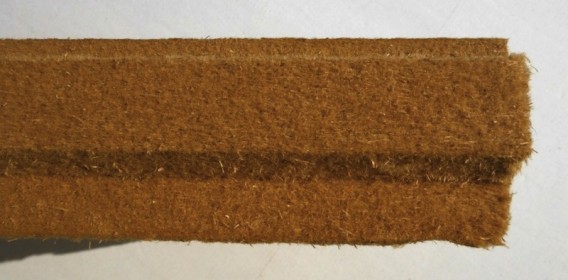
A typical application would be to nail it to the outside of the studs, with just the rainscreen layer on top of it, separated by an air space. The wall’s chief insulation is between the studs, but the Agepan completely covers—and curtails any thermal bridging going through—the structural wood.
Two inches of Agepan THD provides insulation value of R-5.74, and you can slap it on two or three layers thick if you want. It’s quick and easy to put up thanks to the tongue-and-groove edges: pieces don’t have to be cut to end on the studs.
Interestingly, Passive House walls necessarily have an airtight layer, but they may or may not have a water vapor-tight layer. Sam Hagerman of Hammer and Hand in Portland and Seattle is one of many builders in moist climates who prefer vapor-open walls because they dry out better. He tested Agepan by wetting and drying it for two months before deciding to sheathe the Pumpkin Ridge Passive House with it.
“Has it come to this?” you may ask. “They are importing German wood fiber to build with in Portland?” Unfortunately yes. While Europe, with its thousands of Passivhausen under construction annually, has several companies making wood products in this vein, North America currently has none. This would be an easy product for U.S. mills to make, and we have plenty of wood fiber, but it won’t happen until the demand grows considerably.
“It’s probably ten years out,” says Skylar Swinford of Hammer and Hand. “Five if we’re lucky. We builders are all focused on the operational energy savings now, but as things develop we’ll get to looking harder at the embodied energy.”
Energy and carbon emissions that went into a building’s materials and the work of construction are said to be “embodied” in the building. That certainly includes long-distance shipping. (Remember, though, that shipping’s energy is not proportional to distance, since ocean freighters are many times more energy-efficient per ton-mile than, say, trucks.)
The Passive House standard itself looks at operational energy and ignores embodied energy. I assume that isn’t because they don’t care, but because writing clear, specific standards on operational energy is relatively possible. When it comes to embodied energy, everyone can agree that lower is better, and that local is lower than long-distance, all other things being equal, but from there on the measurement of it becomes a can of worms. For example, a gorgeous house project in New Zealand claims Net Zero embodied energy; while I admire many things about that house, I take that claim with a grain of salt.
All the same, many foam insulation materials currently used in the US are thought to have very high greenhouse gas effects during manufacture, probably worse than wood fiber even if its shipped from Germany.