Method Homes is a Seattle manufacturer of modular prefab homes that emphasize sustainability and variety. They currently offer eight different design series from several different architectural firms, and with very distinct styles.
The most striking is their HOMB Series by Skylab Architects, with designs entirely made up of equal-sized equilateral triangles. Echoing Frank Lloyd Wright’s “beehive houses,” HOMBs (a spelling meant to suggest “honeycomb”) have more 60-degree and 120-degree angles than right angles in their floor plans. The model HOMB shown in Portland features custom built-in couches and cushions cut on those same angles.
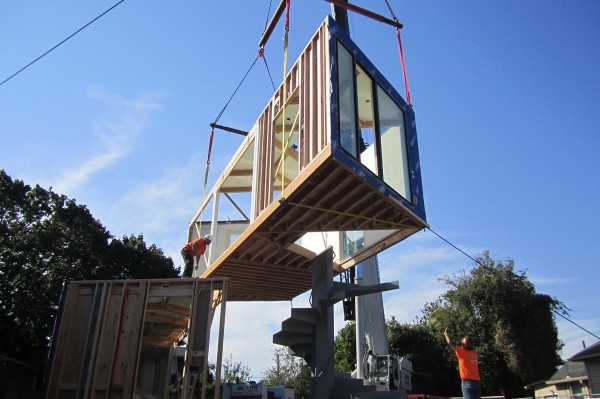
On Method’s new Paradigm Series, a Corten awning adds odd angles, but underneath it all, the modules (like a majority of modules throughout the industry) are simple rectangles sized for easy transport on a flatbed truck. With Paradigm I, II, and III, you get 1, 2 or 3 modules each slightly less than 15 feet wide and more than twice that long.
What most distinguishes Paradigm—a design from Bogue Trondowski Architects—is that it may offer the first modular home on the US market that meets the passive house standard and also goes for six out of seven “petals” of the Living Building Challenge. These standards are tougher to reach than LEED Platinum, a certification also attained by Paradigm but first claimed a year ago by a modular home from competitor Greenfab, also of Seattle.
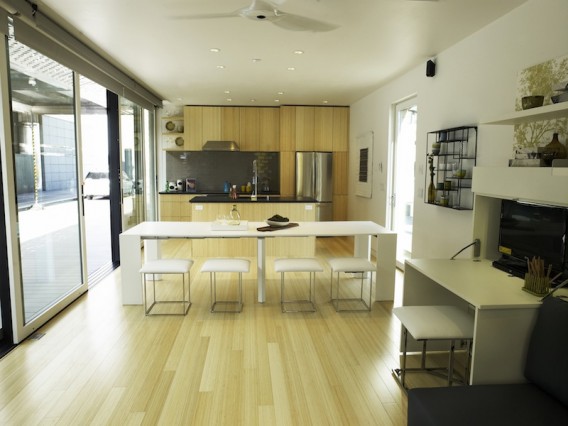
Passive and modular should be a natural fit for each other. As both Method and Greenfab like to emphasize, the biggest advantage of prefab is build quality. Building indoors, you keep all your material dry, so it doesn’t warp, shrink, swell, or support mold cultures that could get sealed up within the walls. Also, building codes require prefab to meet higher structural standards in order to survive the torsional stress of truck transport
So a factory should be the ideal setting for putting together a well-sealed, perfectly insulated building envelope. The reason we’ve waited this long to see a modular prefab PH may just be that the total number of passive houses ordered in the U.S. has been too small to interest mass-production businesses. I expect to see more modular PH offerings before too long. Method Homes is growing rapidly.
A Paradigm I prototype was displayed at the 2012 Greenbuild Expo in San Francisco, and is now for sale for $249,000 to anyone who wants to haul it to their lot. That baby is loaded; its price includes the passive house upgrade, solar panels for net-zero energy and a composting toilet and graywater purification for net-zero water. A base Paradigm I, for $154,000, has thinner walls but still has energy-efficient features like triple-glazed windows and a heat recovery ventilation system.
That would be the “modular” price, covering just what is done in the factory. The estimated “turnkey” price of $209,000 includes delivery, appliances and all construction work at the site, but still does not include permits, fees or utility hookups. Not to mention land.
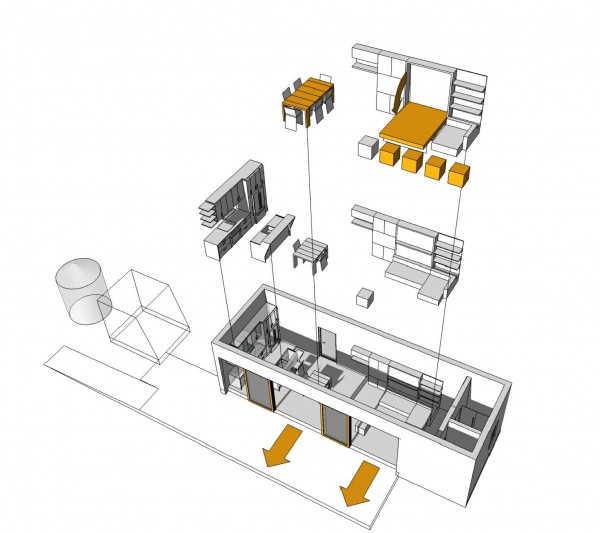
Paradigm 1 is a compact 656 square feet inside‚ essentially a studio apartment house. Paradigm III, 1,868 square feet, starts at $308,220/$420,000. A similar-sized 3-bedroom PH can easily be built in the Puget Sound area for less money—for example, by using SIP panelized construction, which also might be almost as fast as prefab.
Method Homes isn’t trying to be the price leader. They make their case in terms of solidity; of sustainable materials and practice throughout; and of style points—especially for people whose taste is well represented in the pages of Dwell. Prefab can potentially cut costs when that day comes when they’re churning out lots of copies of the same module.